Auszug aus dem elektroModell 4/200 bearbeitet
und ins HTML übersetzt: Peter Rother
Ludwig Retzbach
Brushless News
TORQUEMAX LRK - Sensor- und
bürstenloser Selbsbaumotor
Nein, es handelt sich bei elektroModell
4/2000 nicht etwa neuerdings um das Aprilheft, sondern wie ehedem
um die 4. Ouartalsausgabe. Der Vorschlag, sich seinen Motor einfach
mal selbst zu bauen, ist also kein Scherz. Denn eigentlich war
es schon immer klar: Viel dran ist nicht an so einem Ding, bei
dem ein Permanentmagnet in einem Drehfeld Karussell fährt.
Alles, was dem Verschleiß unterliegt, sind zwei kleine
Kugellager. Lediglich die Fliehkräfte zerren zuweilen unbarmherzig
an den anschmiegsamen Stäbchen aus Neodym. Doch mit dem
entsprechenden Konzept stellt auch dies kein Problem dar. Bei
dem hier vorgestellten Motor handelt es sich nämlich um
einen Außenläufer, bei dem im Betrieb alles dort hin
kommt, wo es hin will: Die Magnete nach außen, die Spulen
nach innen.
Wer ernsthafte Nachbauabsichten verfolgt, sollte allerdings
schon eine Drehbank haben oder wenigstens
einen kennen, der die Kunst spanabhebender Metallbearbeitung
beherrscht. Dabei genügt es noch nicht, wenn alles rund
wird. Im Bereich der Lagersitze ist ein gewisses Maß an
Präzision durchaus erwünscht. Die restlichen Teile
sind handelsüblich (siehe Bezugsquellen). Bliebe noch, die
Motorbezeichnung zu erläutern: TORQUEMAX lässt erahnen,
dass Drehmoment bei der Konstruktionsidee sehr weit oben stand.
Letztere stammt übrigens von Christian
Lucas, der sich professionell mit (meist viel größeren)
Elektromotoren beschäftigt und deshalb eine große
Menge Know-how und Erfahrung in dieses Projekt einbringen konnte.
Emil Kühfuß, gleichfalls
in der Vergangenheit mit Motorenbau befasst, besorgte die Arbeiten
an der Drehbank mit schon gewohnter Präzision und löste
zahlreiche Detailprobleme. Und das dazwischen liegende R (Ludwig Retzbach
anm P.R.) schließlich steuerte ein Zeitgenosse bei,
der das Pflichtenheft formulierte, sich ansonsten bei diesem
fachübergreifenden Unterfangen als eine Art Bindeglied verstand,
ausgestattet mit der Lizenz zum (dumm) Fragen. Zu danken wäre
zudem Walter Fröschle, der
hilfreich im Hintergrund wirkte.
Alles unter Kontrolle
Auch ein sensorloser Brushless-Motor arbeitet nur mit einem
Controller zusammen, mit dem er sich einigermaßen versteht.
Das ist bei handelsüblichen Maschinen nicht anders. Meist
merkt man es schon beim Anlauf, wenn die Partner "es nicht
miteinander können". Jedoch gibt es auch Traumpaare,
die beileibe nicht immer ein und derselben Familie entstammen
müssen. Die TORQUEMAX LRK-Maschinen harmonieren in hervorragender
Weise mit dem Future, dem Controller
aus dem Hause Schulze Electronic, nicht zuletzt dank einer von
Ulf Herder nochmals überarbeiteten Software. Doch scheint
auch eine Seelenverwandtschaft mit dem kurz vor Manuskriptschluss
doch noch lieferbaren actronic-Controller
der Gebr. Köhler zu bestehen (auch mit Speedy-BL
von Jo Aichinger anm P.R). Jedenfalls lief der TORQUEMAX auf
Anhieb damit. Dass es gerade mit diesen beiden Drehfeldstellern
geht, braucht nicht verwundern, schließlich erkennt man
zwischen den Motoren durchaus Parallelen. Dies ist denn auch
der Grund, weshalb es sich lohnt, erst mal die verschiedenen
elektroflugüblichen Motorkonzepte kennen zu lernen. Dieses
bisher bestehende soll und kann der hier veröffentlichte
Bauvorschlag übrigens keineswegs verdrängen, sondern
allenfalls um eine interessante Variante bereichern.
Antriebskonzepte
Angestrebt wird bei gegebener Motorgröße eine hohe
Wellenleistung. Diese ist das Produkt aus Moment
und Drehzahl. In jedem Fall soll möglichst wenig
von der zugeführten Leistung als Wärme verloren gehen.
Wie gut das gelingt, besagt der Wirkungsgrad.
Leider präsentiert sich die Physik als recht unerbittlicher
Verhandlungspartner. Ein mutiger Schritt in die eine Richtung
kostet Zugeständnisse auf der anderen. Am einfachsten ist
eine hohe spezifische Leistung über die Drehzahl zu erreichen.
Meister sind hier die zweipoligen Innenläufer von Lehner oder, davon abgeleitet und produktionsgerecht
modifiziert, die zwischenzeitlich sehr kinderreiche Motorenfamilie
aus dem Hause Hacker.
Bei diesen Maschinen liegen die Spulen nicht in Eisen, sondern
machen es sich im Luftspalt bequem, was die Motorinduktivität
reduziert und damit schnelle Stromwechsel begünstigt. Und
weil der Luftspalt hier ziemlich groß und der Magnetfluss
weitgehend homogen ist, bleiben die bei hohen Drehzahlen steil
ansteigenden Eisenverluste in den Magneten und im äußeren
Rückschluss in Grenzen. Letzteren möchte Harald
Konrath mit seinem Tango-Konzept auch noch ans Leder,
indem er den Rückschluss mitdrehen lässt. Die Motorenrevolution
der südamerikanischen Tänze kommt aber bislang wegen
fehlender Steuerelektronik noch nicht recht aus den Sträuchern.
In jedem Fall wird deutlich, dass die Technik der selbsttragenden
(Luft-)Spule nach einem darauf abgestimmten Controller verlangt.
Als typischer Nachteil ist bei dieser Bauart die begrenzte Kühlung
der Neodymmagnete zu nennen. Und natürlich reichte das Drehmoment
bei den bislang erprobten Maschinen nicht für den direkten
Antrieb großer Propeller.
Den systemtechnischen Gegenpol hierzu bilden die Multipolmaschinen
der Herren Köhler und Plettenberg. Beim actro-Außenläufer
sorgt das 8-Pol-Konzept für hohes Drehmoment und außen
liegende Magnete für ihre eigene Kühlung. Als Nachteil
sind der aufwendig zu bewickelnde, sehr spezielle Blechschnitt
und die noch relativ langen Eisenwege zu betrachten, auf denen
das Magnetfeld verläuft. Letztere gelingt es Plettenberg
bei der 10-Pol-"Waschmaschine" zwar ein wenig zu straffen,
allerdings um den Preis eines noch größeren Bauaufwands
und einer sehr mäßigen internen Raumausnutzung. Das
Innenläuferprinzip mit großem Rotordurchmesser erzeugt
zudem Fliehkräfte, bei denen man die Magnete bei hoher Drehzahl
festbinden muss.
Drehmomentmaschinen werden also teuerer und glänzen im
direkten Vergleich mit nicht ganz so hohen Wirkungsgradwerten,
allerdings in belden Fällen nur so
lange, wie man das Getriebe nicht mitrechnet. In der Praxis
hat das Schnellläufer- Getriebe-Konzept bei der möglichen
Leistungsdichte die Nase vorn, wovon vor allem der sportliche
Wettbewerb profitiert. Ein Direktantriebsmotor hingegen präsentiert
sich als pflegeleichter und letztendlich nicht minder effizient,
denn es gibt nur wenige Getriebe, die sich mit "Provisionen"
unter 5% zufrieden geben.
Der "TDI" Motor
Der hier vorgestellte Selbstbaumotor stellt einen 14-poligen
Außenläufer dar. Zusammen mit einem 12-teiligen
Stator ergibt sich bei jedem Drehwinkel eine hohe Überdeckung
(geringe Polentfernung bedeutet hohe Anziehungskraft). Die herausragende
Besonderheit der neuartigen Antriebslösung liegt wohl in
der äußerst kompakten Bauweise und dem daraus resultierenden
niedrigen Gewicht. Die bislang unüblich
hohe Polzahl steht für ein gesteigertes Drehmoment bei niedrigen
Windungszahlen, d.h. auch niedrige spezifische Drehzahl (ns)
gleichzeitig geringem Ri. Die Maschine erreicht damit nicht nur
eine hohe Leistungsdichte (W/kg)
, sondern mehr noch eine hervorragende
Drehmomentdichte (Nm/kg). Salopp formuliert, könnte
man vom TDI unter den Elektromotoren sprechen. Auch der Wirkungsgrad
der Selfmade-Maschine braucht sich nicht vor der Serienkonkurrenz
zu verstecken, wenn gleich dem aufmerksamen Leser bereits klar
sein dürfte, dass eine derart konsequente Optimierung in
Richtung Drehmoment nicht gleichzeitig Eta-Spitzenwerte hervorzaubern
kann. Vergleichsmessungen mit Propellern bekannter Leistungsaufnahme
(Aeronaut-CAM- Carbon-Serie) ergaben bei den noch etwas sehr
"hand- geschnitzt" wirkenden Prototypen Wirkungsgradwerte
knapp unter 80%, mit einem allerdings sehr breit angelegten Maximum.
Genauere
Leistungsmessungen waren noch nicht möglich, da sich das
neue Motorkonzept bislang noch ziert, sich von den für Innenläufermaschinen
ausgelegten Motorprüfständen in die Karten schauen
zu lassen (Montageproblem). Die Hauptverlustquelle bei diesem
einfach gebauten Motor bildet derzeit noch der Eisenkreis, dessen
Optimierungspotentiale wohl noch nicht gänzlich ausgeschöpft
sind, während die Kupferverluste hier nur wenig ins Gewicht
fallen.
Die Outdoorlösung
Der Stator basiert auf 12-teiligen
Blechschnitten, wie sie bei herkömmlich kohlebestromten
Motoren der Firmen Bühler (großer
Carrera-Motor), Plettenberg (Serie
32 bzw. ULTRA 1600 bzw. Evo) oder auch beim Newtor
verwendet wurden. Der Trick: Es wird jeweils nur jeder zweite
Ankerzahn bewickelt. Das lässt sich, wie der Autor erfahren
konnte, nach kurzer Einübung leicht selbst bewerkstelligen,
denn es sind jeweils nur wenige Windungen aufzubringen. Wicklungsübergriffe
auf Nachbarzähne, wie sonst üblich, entfallen. Damit
bleiben auch die verlustbringenden Wickelköpfe (das sind
die Drahtwülste an den Stirnseiten der Bleche) in Grenzen.
Das hilft, die TORQUEMAX-Maschine so kompakt zu konstruieren,
dass sie eigentlich nicht mehr eingebaut werden muss; man kann
sie in vielen Fällen auch anbauen. Die dadurch zustande
kommende extreme Lage hilft bisweilen, den Schwerpunkt einzuhalten,
denn die beiden ersten, noch keineswegs gewichtsoptimierten Prototypen
bringen gerade mal 128 Gramm
auf die Waage. Berechnet wurden sie für eine elektroflugtypische
(!) Dauerausgangsleistung von 450 Watt,
jedoch haben sie bei Flugerprobungen auch schon 550 bis 600 Watt
klaglos und erstaunlich "cool" überstanden (siehe
unten).
Als "gesundheitsfördend" erweist sich auch bei
diesen Motoren ausreichend viel frische Luft, was sich allerdings
angesichts der besonderen, propellernahen Arbeitsweise auch kaum
vemeiden lässt. Die Luftschraube sitzt nämlich unmittelbar
auf dem Rotor, braucht also auch keinen Mitnehmer. Allerdings
muss die Zentral bohrung bei derzeitigem Stand der Technik von
10 auf 12 mm erweitert und durch zwei dezentrale Mitnehmerlöcher
ergänzt werden. Auch Klappluftschraubenmitnehmer sind auf
diese Weise leicht anzubringen. Schließlich kann (praktische
Erprobung steht noch aus) der TORQUEMAX sogar voll in den Spinner
integriert werden, was einer kompletten "Outdoor-Lösung"
des Antriebsproblems gleichkäme.
Der Autor sieht die hier vorgestellte Lösung keineswegs
als abgeschlossene Entwicklung an. Es lässt sich an vielen
Stellen noch Gewicht einsparen, ohne die Stabilität der
Konstruktion in fahrlässiger Weise zu gefährden. Bei
der hier vorgestellten Weiterentwicklung (TORQUEMAX
LRK 320/12-17) kommt trotz gewachsener Magnetlänge
die Briefwaage schon bei 119 Gramm
zum Stillstand. Modelltechnische Weightwatcher mit Mut zum Experiment
werden schnell zusätzliche Einsparungspotentiale entdecken,
wie etwa Ausfräsungen der Lagerschilde, Hohlachse oder den
(zumindest partiellen) Ersatz von Alu durch CfK. Wer letzte Hemmungen
über Bord wirft, spart sich das hintere Lagerschild und
klebt die (vielleicht etwas verlängerte) Achse direkt am
Motorspant fest.
In einer späteren Folge ist geplant, einen Motor mit
größerem Statordurchmesser und/oder größerer
Magnetlänge (für den KW-Bereich) vorzustellen, der
sich derzeit in Erprobung befindet. Dann sollen auch "exotische"
Einbau- und Einsatzmöglichkeiten diskutiert werden.
Und nun schnell noch etwas Theorie
In einer Zeit, in der es alles schon fertig zu kaufen gibt,
macht der Selbstbau von modelltechnischen Komponenten nur Sinn,
wenn diese dadurch noch besser auf die individuellen Bedürfnisse
abgestimmt werden können. Hier also kurz einige Fingerzeige,
wie man sich seinen "Maßmotor"
berechnen kann. Da dies üblicherweise sehr kompliziert
abläuft, sei hier ein von Christian Lucas erprobtes vereinfachtes
Drehmoment-Berechnungsverfahren vorgestellt. Hierbei wird lediglich
der magnetische Kreis betrachtet. Die elektrischen Werte bleiben
erst mal außen vor. Als Musterpropeller dient die CAMcarbon-Serie
von Aeronaut, nicht allein wegen ihrer unbestrittenen Güte,
sondern vor allem deshalb, weil allein diese Firma auch Leistungskennwerte
herausgibt. Die vom magnetisierten Polschuh auf die Läufermagnete
ausgeübte Kraft F ist der magnetischen Flussdichte B im
Luftspalt und der Eisenfläche A proportional und beträgt
F = A x 4 B ^ 2
Bei einem für die verwendeten Neodymmagnete angenommenen
B = 1 T (sichere Annahme) würde die Kraft bei 4 N/cm2 liegen.
Da jedoch maximal 65% der Umfangsfläche mit Magneten belegt
werden sollten (sonst liegen die einzelnen Pole zu nah beieinander),
gehen wir im Weiteren von nur 0,65 x 4 N/cm2 = 2,6 N/cm2
aus. Bei der Mustermaschine mit 32 mm Statordurchmesser und 10
mm Magnetlänge beträgt diese Fläche
A = 2r x 7t x I = 10,05 cm2
Die Kraft im Luftspalt liegt also bei
F x A = 26 N
Das Drehmoment, das der Motor mit 16 mm Statorradius hervorzubringen
imstande ist, beziffert sich damit auf
M = F x r = 26 N x 0,016 m = 0,42 Nm
Dieses Drehmoment kann die Maschine
unter maximaler Belastung theoretisch bei jeder Betriebsdrehzahl
abgeben.
Umgesetzt in die fliegerische Praxis bedeutet dies: Ein Drehmoment
von 0,42 Nm ist erforderlich, um eine Aeronaut CAM-Carbon-Luftschraube
der Größe 9,5 x 5 (n1oo = 8100 min-1) in
eine Drehzahl von 15 287 min-1 zu versetzen. Bei der 8 x 5
aus gleichem Hause (n100 = 10 150 min-1) reicht das Drehmoment
rechnerisch für 21 444 min-1; bei einer 16 x 10
(n100 = 3500 min-1) sind es noch 4342 min-1. Das ist (im
Direktantrieb!!) schon eine Menge Holz für ein Motörchen,
das mit ca. 120 Gramm Masse etwa in der Klasse eines SPEED 480
antritt!
Die Leistung, welche der Motor dabei abgibt, ist nun natürlich
wieder mit von der Drehzahl abhängig.
Luftschr |
Leist.in Watt |
8 x 5 |
943 |
9,5 x 5 |
672 |
11 x 7 |
472 |
14 x 8 |
272 |
16 x 10 |
191 |
18 x 11 |
163 |
In der Praxis wird man es ganz so bunt nicht treiben, sondern
mit Rücksicht auf den Wirkungsgrad es bei Drehzahlen von
max. 15000 min-1 (Eisenverluste!)
belassen und vielleicht auch nur 80 bis 90% des möglichen
Drehmoments ausnutzen.
Windungsberechnung
Wie bei jedem Elektromotor setzt sich auch beim TORQUEMAX
die Eingangsleistung aus U x I zusammen,
wobei mehr Spannung (U) auch hier besser ist als zu viel Strom
(I). Die "Spannungsklasse" des Motors ergibt sich aus
seiner Windungszahl. Sie wird am besten empirisch ermittelt.
Dazu bewickelt man einen Ankerzahn probeweise mit z.B. 10 Windungen,
baut den Motor zusammen, steckt den Lagerzapfen in das Dreibackenfutter
einer Bohrmaschine und lässt das Ganze bei mittlerer Drehzahl
laufen. Man misst Drehzahl (mit hilfe einer Reflexmake am Motorgehäuse)
und die sich ergebende Generatorwechselspannung (Veff). Letzerer
Wert wird erst mal verdoppelt, da später 2 Zähne in
Reihe liegen. Ein Zuschlag von 15 bis 20%
gleicht die Betriebsverluste aus.
Misst man beispielsweise 3 Veff, so ergibt sich damit ein
Rechenwert von ca. 7 V. Ein 7-Volt (= Zellen)-Motor müsste
somit also ein 10-Winder sein. Sind z.B. 14 V Betriebsspannung
gewünscht, sind 20 Windungen vorzusehen (usw.).
Schief gewickelt
Könnte man so gar nichts falsch machen, es wäre
kein Spaß dabei. Doch sorgt der Zusammenbau des Stators
und vor allem dessen Bewicklung für die nötigen Akzente.
Wenn möglich, sollte das Statorpaket aus mög1ichst
vielen dünnen Blechen bestehen. Die Anzahl ergibt sich aus
der gewünschten Länge und entspricht der verfügbaren
Magnetlänge. Diese sollte 70% des Statordurchmessers nicht
überschreiten (UD< 0,7).
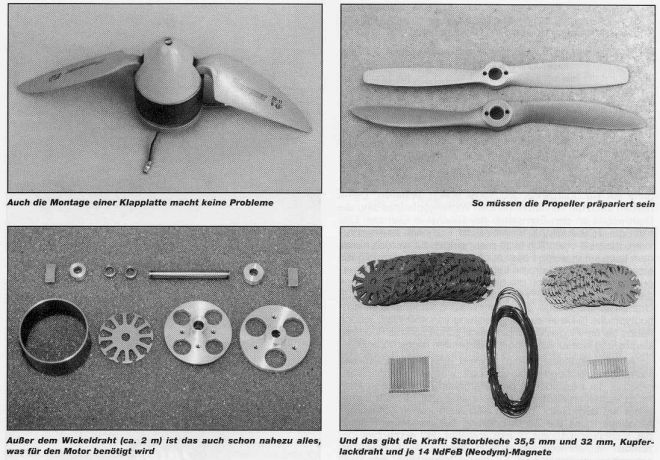
Die Bleche mit 5 mm Lochdurchmesser werden positionsgerecht
"aufgefädelt", sauber ausgerichtet (Zahn 1 weist
oben eine Vertiefung auf) und auf der Stahlachse mit Loctide
601 verklebt. Danach empfiehlt es sich, die Wickel kanten der
äußeren Bleche mit einer Nadelfeile zu brechen. Dies
hilft später Masseschlüsse zu vermeiden. Zusätzlich
muss der Wickel raum isoliert werden. Viele schwören auf
eine angetrocknete Schicht von dickflüssigem Sekunden kleber;
Isolierlack alleine bildet jedenfalls keinen hinreichenden Schutz.
Motorenbauer verwenden hier dünne, hitzebeständige
Folien, die man mit etwas Übermaß zuschneidet und
so in die zu bewickelnden Nuten legt, sodass sich ein seitlicher
Überstand ergibt, den man um die Stirnseiten herumbiegt.
Wer über etwas Geduld verfügt, kann die Nuten auch
mit mindestens zwei Schichten temperaturbeständiger Klebefolie
(z.B. GOLDfix-Kaptonband von Kontronik) "auspflastern".
Trotz aller Vorkehrungen sollte nach dem Bewickeln immer mit
einem Ohmmeter auf eventuelle Schlüsse geprüft werden.
Das Wickeln selbst hat sich, trotz
zwischenzeitlich durchaus vorhandener Übung, bislang nicht
zur lieblingsbeschäftigung des Autors entwickelt. Dieser
musste zudem erfahren, dass selbst ausgesprochen langweilige
Fernsehsendungen sich dafür keineswegs als begleitende Unterhaltung
eignen. Vielmehr empfiehlt sich eine verschärfte Kellerklausur
mit umgeleitetem Telefon. Zwar ist es dem Motorstrom und dem
daraus resultierenden Magnetfeld ziemlich egal, ob die Wicklung
nachher "schön" aussieht. Auch spielt die mechanische
Festigkeit beim Stator eine untergeordnete Rolle. Doch dankt
es der Motor im späteren Betrieb sehr, wenn alle Spulen
genau die gleiche Windungszahl haben. Und da man im Interesse
eines guten Wirkungsgrads den vorhandenen Wickelraum möglichst
immer ausnutzen sollte, kann es nicht schaden, zumindest bei
den ersten bei den Lagen Windung an Windung zu legen. Das kostet
Zeit und hinterlässt tiefe Fingerstriemen. Doch es lohnt
sich!
Bei der gegebenen Größenordnung hat sich bis 250
°C hitzefester Polyamidlackdraht
bewährt. Die Mustermaschine wurde mit 17 bzw. 20 Windungen
von 0,654 mm Durchmesser gewickelt.
Probeweise entstand auch eine 7-Windungs-Variante mit zwei parallelen
Drähten gleichen Durchmessers. Den
besseren Füllfaktor erreicht man jedoch stets mit einem
dicken Draht, der sich allerdings bei größeren
als den angegebenen Stärken bald nicht mehr sauber einlegen
lässt. Da die verwendbaren Blechschnitte in puncto Wickelraum
etwas differieren, wird man wohl auch hier über einige Versuche
seinem Ziel am nächsten kommen.
Wickelschema
Das Wickelschema selbst ist im Bild wiedergegeben. Dabei sind
die jeweils gegenüberliegenden Spulen mit umgedrehtem Wickelsinn
in Reihe geschaltet. Man beachte, dass die Verbindung zwischen
den jeweils gegenüberliegenden Spulen nicht zu straff anliegt,
damit sie um den Flasch der Trägerplatte herumgeführt
werden kann. Für Maschinen, die mit sehr niedriger Spannung
laufen sollen, lassen sich diese magnetischen Antipoden auch
(unter Beachtung der Stromrichtung!) parallel schalten. Außerdem
kann man von der eingezeichneten Dreieckschaltung der drei Windungsstränge
auch auf Sternschaltung wechseln. Damit reduziert man die spezifische
Drehzahl nochmals um den Faktor 1,73.

Und dann bauen wir ihn einfach
zusammen
Prinzipiell ergibt sich der Zusammenbau
aus den jeweiligen Konstruktionszeichnungen. Zuerst wird der
bewickelte Stator plus Alu-Distanzring mit der 5-mm-Stahlachse
gut verklebt. Die Trägerplatte klemmt mit einer M3-Madenschraube
auf der Achse und bleibt so abnehmbar. Das Einkleben der Magnete
in den Weicheisen-Rückschlussring (St 38) besorgt man mit
Sekunden kleber oder -noch komfortabler -mit Loctide 326 Kleber
plus Aktivator 7649. Man beachte, dass die Magnete den Eisenring
nur mit den Kanten berühren. Auf die Einhaltung der genauen
Abstände kommt es ebenso an wie auf die exakt axiale Ausrichtung
der Magnetstreifen. Bewährt hat sich hier die Zweckentfremdung
eines Papiermeterstabs aus dem Möbelhaus. Damit legt man
die Lage jeweils einer Magnetkante genau fest. Zwecks axialer
Ausrichtung fertigt man eine 90°-Lehre aus biegsamer Folie,
die innenseitlg angelegt werden kann. Die Magnete fluchten rückseitig
mit dem Eisenring.
Verwendbar sind NdFeB-Magnete der Breite 5 bis 6 mm und 2
bis 2,5 mm Dicke. Von Letzterer hängt der Durchmesser des
Eisenrings und damit des Rotorträgers ab. Das Design geht
von 0,5 mm Luftspalt aus. Dieser sollte keinesfalls unterschritten
werden, zumal er durch die kreissehnenförmige Anordnung
der Magnetplättchen mechanisch bereits eingeengt ist. Bei
6 mm Magnetbreite kann es nicht schaden, dem Luftspalt beidseitig
noch 0,1 bis 0,2 mm zu spendieren. Ein vergrößertes
Luftspaltmaß kostet zwar Drehmoment, verringert aber (zumal
bei höherer Drehzahl) die Eisenverluste des Motors oft beträchtlich.
Sollte die gewünschte Magnetlänge nicht erhältlich
sein, kann man sie problemlos der Länge nach anreihen. Dies
reduziert sogar die Wirbelstromverluste. Notfalls lassen sich
die Plättchen sogar kürzen. Allerdings sind derartige
Jobs nicht vergnügungssteuerpflichtig. Rückschluss
und Rotorträger werden genau wie die Magnete verklebt. Nicht
einzukleben braucht man hingegen die Kugellager, wenn der Presssitz
genau stimmt. Sie lassen sich so bei Bedarf auch leichter wechseln.
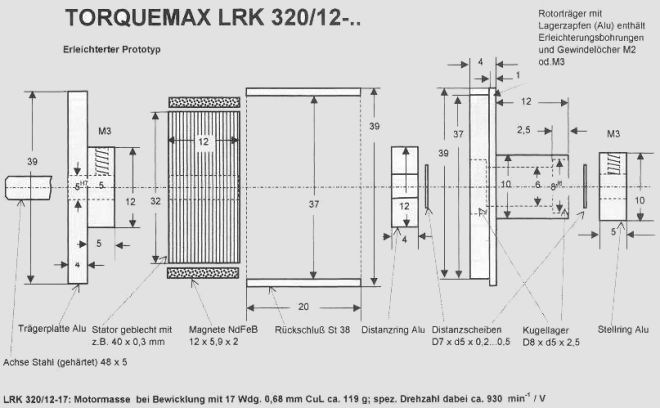
Bezugsquellen
Verwendet wurden bei den Prototypen Kugellager der Dimension
10 mm x 5 mm x 4 mm (Kyosho Nr. 1901). In diesem Falle bekommt
der Lagerzapfen jedoch 12 mm Durchmesser, was eine entsprechende
Aufweitung der Propellerbohrung bedingt. Später kamen dann
8 mm x 5 mm x 2,5 mm Schmal ringkugellager (Kyosho Nr. 1902)
zum Einsatz. Damit lässt sich der Lagerzapfen auf 10 mm
reduzieren. Vorteil: Die handelsüblichen Alu-Klappluftschrauben-Mitnehmer
mit 12 mm Breite und 8er-Bohrung vertragen problemlos eine entsprechende
Aufbohrung. Im Normalbetrieb sind die Lager gering belastet,
da die Luftschraube genau zwischen beiden Lagern sitzt und eventuelle
Unwuchten (pfui!) hier nicht über einen Hebelarm wirken.
Auch die Distanzscheibchen sind im
Kyosho-Programm zu finden (Nr. 96643).
Der Versuch, die Magnete in den erforderlichen Kleinmengen
zu beziehen, wird nur in seltenen Fällen mit spontanen Freundschaftsbezeugungen
quittiert und erfordert mitunter ein gewisses Maß an Überzeugungskraft.
In "Härtefällen" hilft der Autor mit Magneten
(12 mm x 5,9 mm x 2 mm bzw. 24 mm x 5,9 mm x 2 mm) und 32- bzw.
35,5-mm Blechschnitten gegen Erstattung der Selbstkosten weiter
(Verlagsadresse). Ansonsten sei genannt:
IBS Magnet
Kurfürstenstr. 92
D-12105 Berlin
http://www.ibsmagnet.de
Vacuumschmelze
Postfach
D-63412 Hanau
Magnetfabrik Schram berg
Max-Plank-Str. 15
D- 78713 Schramberg-Sulgen
Tridelta Magnetsysteme GmbH
Ostkirchenstr. 177
D-44287 Dortmund
Der HTML-Ersteller hat auch einen
LRK350-20, diesmal mit drehender Welle erstellt und ist begeister,
wie gut der Motor dreht.
LRK350-20-15.html |